Диагностика пневмоприводной арматуры с использованием интеллектуальных позиционеров
Сегодня практически у любого производителя позиционеров присутствует линейка цифровых продуктов, обладающих функциями диагностики. Поэтому заказчику, который впервые принимает решение о внедрении арматуры с функцией диагностики на своем предприятия, очень сложно определиться с выбором конкретного решения. Рассмотрим сильные и слабые стороны различных типов диагностики.
Практически в любом современном позиционере, как минимум, имеется возможность накопительной диагностики и самодиагностики. Дополнительно к этому позиционеры могут обладать возможностью построения диагностических графиков, которые позволяют оценивать техническое состояние оборудования
Накопительная диагностика
Накопительная диагностика предоставляет информацию о следующих особенностях работы отдельно взятого клапана:
в энергонезависимой памяти.
Анализ этой информации помогает:
износу, находится в неудовлетворительном состоянии. Его технические характеристики могут полностью соответствовать требованиям изготовителя арматуры, и работать он будет не хуже клапана, подвергшегося меньшему износу. Поэтому данный тип диагностики рекомендуется использовать для сравнения общего технического состояния арматуры только при отсутствии других инструментов.
При этом накопительная диагностика просто незаменима при определении ресурса сальников и сильфонов (таблица).
В идеале на предприятии должен быть менеджер ресурсов, в котором для каждой позиции задан ресурс сальника, сильфона, и есть возможность вводить информацию о техническом обслуживании, ремонте арматуры. Программное обеспечение должно автоматически по расписанию подключаться к позиционерам, производить расчет оставшегося ресурса и выдавать оператору рекомендации о том, какой узел на какой позиции потребует замены в ближайшее время.
Преимущества накопительной диагностики:
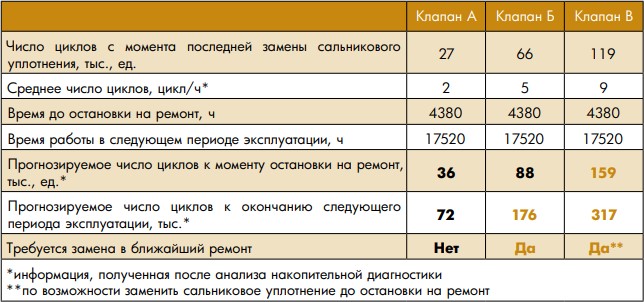
Таблица 1. Использование накопительной диагностики для определения необходимости замены сальникового уплотнения с ресурсом 100 тыс. циклов
Самодиагностика позиционера/индикаторы состояния/сигнализация об ошибках
Современные цифровые позиционеры осуществляют мониторинг различных параметров, которые связаны как с работой самого позиционера, так и с работой клапана/привода. Ошибка позиционирования, низкое давление воздуха КИП, отказ встроенных в позиционер датчиков, сбои в его памяти, ошибки в электронике или во внутреннем ПО — это лишь некоторые из них. Сигнализация о выявленных неисправностях может осуществляться как с помощью программных средств, так и с помощью встроенных дискретных выходов. При возникновении ряда критических ошибок позиционер переходит в отказобезопасный режим и переводит клапан в безопасное положение. Для определенного типа позиционеров (например, для аварийных отсекателей) переход в отказобезопасный режим может быть отключен.
Чем больше параметров контролирует позиционер, тем шире диагностическое покрытие, и тем выше шанс выявить неисправность на ранней стадии, как правило, до появления более серьезных нарушений в работе клапана.
В идеале менеджер ресурсов должен с высокой частотой опрашивать позиционеры на наличие сигналов об ошибках, а в случае их обнаружения заносить информацию в журнал и информировать оператора.
Преимущества самодиагностики:
При этом самодиагностика не предназначена для оценки технического состояния клапана или привода.
Диагностические графики арматуры выведенной из ТП
Диагностические графики арматуры выведенной из ТП позволяют наиболее точно оценить текущее техническое состояние клапана. Для проведения таких тестов требуется вывести арматуру из ТП, так как в ходе построения графиков позиционер перестает реагировать на управляющий сигнал от системы и полностью закрывает/открывает клапан. В ходе тестов определяются следующие параметры: линейность, гистерезис, точность регулирования, трение, фактический диапазон пружин привода, зона нечувствительности, разрешающая способность клапана, переход за заданное значение (Overshoot), время полного открытия/закрытия, время реакции, T86 и т.д. Для определения трения и фактического диапазона пружин привода позиционер должен иметь датчик давления воздуха в приводе.
Анализируя графики, можно сделать заключение о качестве регулирования, о состоянии плунжерной пары, определить износ элементов конструкции, наличие посторонних предметов в затворе, задиров на штоке/валу, утечек воздуха в обвязке привода, повреждения пружинного блока, мембраны привода и т.п. Если возможно провести снятие диагностических графиков до остановки оборудовании на ремонт (например, есть байпасная линия), то анализируя их и сравнивая с предыдущими и начальными графиками, предоставляемыми производителем арматуры, можно оценить текущее состояние клапана, определить какие запасные части могут потребоваться при обслуживании данной позиции и на основе этой информации заказать их заранее, определить требуемый объем ремонтных работ и спрогнозировать использование людских ресурсов.
Преимущества данного подхода:
Ни один из рассмотренных выше методов получения диагностической информации не обеспечивает мониторинга технического состояния регулирующей арматуры в РВ. При этом потребители хотят видеть систему, которая обладает следующими свойствами:
На данный момент лишь несколько ведущих компаний в мире обладают технологиями, позволяющими создавать такие системы. Это объясняется тем, что для получения информации о работающих позициях необходимо подключаться к ним и наблюдать за их работой, а не искусственно создавать оптимальные условия для получения диагностической информации, как в случае с построением диагностических графиков. При этом клапан может большую часть времени перемещаться в пределах нескольких процентов, что делает невозможным применение классических методов анализа диагностических данных.
Производитель должен разработать математические модели работы регулирующей арматуры, которые могли бы с высокой точностью определять техническое состояние оборудования даже по таким незначительным перемещениям. Он должен описать ключевые индикаторы состояния (Key Perfomance Indicators, KPI, например, трение, фактический диапазон пружины, время отклика и т.п.), которые были бы явно связаны с изменением технического состояния оборудования, и добиться того, чтобы рассчитанные на основе математических моделей значения не зависели от амплитуды изменения управляющего сигнала. То есть для одного и того же клапана необходимо всегда получать очень близкие значения индикаторов KPI как при амплитуде в 0,3…0,5…0,9%…, так и при амплитуде в 10…15…25%… и т.д.
Для реализации этой задачи должен быть разработан программный продукт, который по расписанию с заданным временным интервалом подключается ко всем цифровым позиционерам и определенное время отслеживает работу арматуры. Затем он автоматически рассчитывает индикаторы, связанные с техническим состоянием оборудования, сохраняет их в БД, определяет наличие отклонений от нормы, и в случае выявления неисправности информирует о ней оператора с указанием возможных причин ее появления и способов устранения. Только в этом случае возможно получить непрерывную диагностику работающего оборудования и по максимуму задействовать функции современных цифровых позиционеров. Желательно, чтобы в такой системе для любой позиции была возможность просмотра сборочных чертежей и определения артикульных номеров запасных частей.
Если на предприятии уже используются цифровые позиционеры с функциями диагностики, основные затраты при внедрении такой системы будут связаны с покупкой лицензии и с первичной настройкой. В ходе такой настройки для каждой позиции определяются допуски по каждому индикатору KPI. Да,здесь, как правило, не обойтись без привлечения специалистов поставщика оборудования/системы диагностики, но когда система настроена, затраты, связанные с ее обслуживанием, практически отсутствуют, так как не требуется персонал, обладающий глубокими познаниями в сфере диагностики, а основная часть операций выполняется в автоматическом режиме.
Преимущества подхода:
Таким образом, если на предприятии с помощью диагностики планируется только определять износ сальникового уплотнения или контролировать исправность самого позиционера, то нет смысла приобретать дорогие позиционеры с расширенными диагностическими функциями.
Если же требуется хороший инструмент для оценки технического состояния регулирующей арматуры на время ремонтов, тот здесь не обойтись без позиционеров, которые могут строить диагностические графики. При этом стоит отдавать предпочтение продуктам, которые могут строить график зависимости положения клапана от давления в приводе, и обладают встроенными датчиками давления на выходе.
В случаях, когда принято решение постоянно следить за изменением технического состояния оборудования, стоит обратить внимание на позиционеры с расширенными диагностическими функциями и системы on-line диагностики. И если на предприятии эксплуатируются позиционеры нескольких производителей, то желательно выбирать программные продукты, которые могут работать одновременно со всеми имеющимися позиционерами.
Практически в любом современном позиционере, как минимум, имеется возможность накопительной диагностики и самодиагностики. Дополнительно к этому позиционеры могут обладать возможностью построения диагностических графиков, которые позволяют оценивать техническое состояние оборудования
Накопительная диагностика
Накопительная диагностика предоставляет информацию о следующих особенностях работы отдельно взятого клапана:
- сколько времени он находился в закрытом/открытом положении;
- сколько времени он находился в положении близком к закрытому;
- сколько циклов отработал клапан;
- суммарный ход клапана (чем он выше, тем больше износ оборудования).
в энергонезависимой памяти.
Анализ этой информации помогает:
- выявлять ошибки выбора арматуры;
- определять оставшийся ресурс сальникового уплотнения, сильфона и т.п.;
- при отсутствии других диагностических инструментов определять арматуру, которой при следующей плановой остановке на ремонт необходимо будет уделить повышенное внимание.
износу, находится в неудовлетворительном состоянии. Его технические характеристики могут полностью соответствовать требованиям изготовителя арматуры, и работать он будет не хуже клапана, подвергшегося меньшему износу. Поэтому данный тип диагностики рекомендуется использовать для сравнения общего технического состояния арматуры только при отсутствии других инструментов.
При этом накопительная диагностика просто незаменима при определении ресурса сальников и сильфонов (таблица).
В идеале на предприятии должен быть менеджер ресурсов, в котором для каждой позиции задан ресурс сальника, сильфона, и есть возможность вводить информацию о техническом обслуживании, ремонте арматуры. Программное обеспечение должно автоматически по расписанию подключаться к позиционерам, производить расчет оставшегося ресурса и выдавать оператору рекомендации о том, какой узел на какой позиции потребует замены в ближайшее время.
Преимущества накопительной диагностики:
- предусмотрена в любом цифровом позиционере;
- накопление, получение, анализ диагностических данных не влияют на работу клапана, можно использовать на работающих установках;
- позволяет заранее определять потребность замены сальникового уплотнения, сильфона, и заблаговременно заказывать требуемые запасные части на склад.
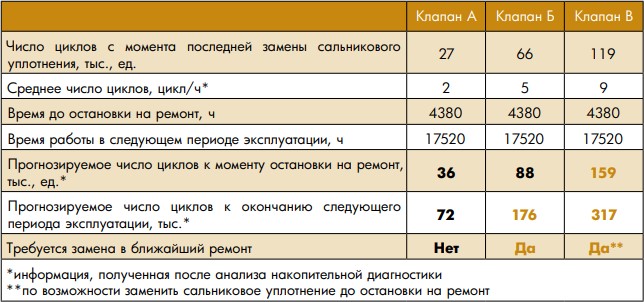
Таблица 1. Использование накопительной диагностики для определения необходимости замены сальникового уплотнения с ресурсом 100 тыс. циклов
Самодиагностика позиционера/индикаторы состояния/сигнализация об ошибках
Современные цифровые позиционеры осуществляют мониторинг различных параметров, которые связаны как с работой самого позиционера, так и с работой клапана/привода. Ошибка позиционирования, низкое давление воздуха КИП, отказ встроенных в позиционер датчиков, сбои в его памяти, ошибки в электронике или во внутреннем ПО — это лишь некоторые из них. Сигнализация о выявленных неисправностях может осуществляться как с помощью программных средств, так и с помощью встроенных дискретных выходов. При возникновении ряда критических ошибок позиционер переходит в отказобезопасный режим и переводит клапан в безопасное положение. Для определенного типа позиционеров (например, для аварийных отсекателей) переход в отказобезопасный режим может быть отключен.
Чем больше параметров контролирует позиционер, тем шире диагностическое покрытие, и тем выше шанс выявить неисправность на ранней стадии, как правило, до появления более серьезных нарушений в работе клапана.
В идеале менеджер ресурсов должен с высокой частотой опрашивать позиционеры на наличие сигналов об ошибках, а в случае их обнаружения заносить информацию в журнал и информировать оператора.
Преимущества самодиагностики:
- предусмотрена в любом цифровом позиционере;
- накопление, получение, анализ диагностических данных не влияют на работу клапана, можно использовать на работающих установках;
- позволяет выявлять неисправности в работе позиционера, проблемы с линией воздуха КИП.
При этом самодиагностика не предназначена для оценки технического состояния клапана или привода.
Диагностические графики арматуры выведенной из ТП
Диагностические графики арматуры выведенной из ТП позволяют наиболее точно оценить текущее техническое состояние клапана. Для проведения таких тестов требуется вывести арматуру из ТП, так как в ходе построения графиков позиционер перестает реагировать на управляющий сигнал от системы и полностью закрывает/открывает клапан. В ходе тестов определяются следующие параметры: линейность, гистерезис, точность регулирования, трение, фактический диапазон пружин привода, зона нечувствительности, разрешающая способность клапана, переход за заданное значение (Overshoot), время полного открытия/закрытия, время реакции, T86 и т.д. Для определения трения и фактического диапазона пружин привода позиционер должен иметь датчик давления воздуха в приводе.
Анализируя графики, можно сделать заключение о качестве регулирования, о состоянии плунжерной пары, определить износ элементов конструкции, наличие посторонних предметов в затворе, задиров на штоке/валу, утечек воздуха в обвязке привода, повреждения пружинного блока, мембраны привода и т.п. Если возможно провести снятие диагностических графиков до остановки оборудовании на ремонт (например, есть байпасная линия), то анализируя их и сравнивая с предыдущими и начальными графиками, предоставляемыми производителем арматуры, можно оценить текущее состояние клапана, определить какие запасные части могут потребоваться при обслуживании данной позиции и на основе этой информации заказать их заранее, определить требуемый объем ремонтных работ и спрогнозировать использование людских ресурсов.
Преимущества данного подхода:
- наиболее точный метод определения технического состояния оборудования;
- позволяет выявлять неисправности в работе привода, клапана, позиционера;
- позволяет определить причины возникших неисправностей.
- позиционеры с данным типом диагностики стоят дороже;
- накопление, получение, анализ диагностических данных влияют на работу клапана, требуется выведение арматуры из ТП;
- для анализа графиков требуется наличие квалифицированного, опытного специалиста.
Ни один из рассмотренных выше методов получения диагностической информации не обеспечивает мониторинга технического состояния регулирующей арматуры в РВ. При этом потребители хотят видеть систему, которая обладает следующими свойствами:
- возможность работы с позиционерами любого производителя;
- работа с позиционерами только в режиме чтения (не должно быть даже теоретической возможности повлиять на работу основной системы управления или позиционеров);
- автоматический сбор и анализ диагностической информации в РВ;
- автоматический контроль технического состояния оборудования в РВ;
- автоматическое определение основных причин возникших неисправностей с указанием способов их устранения.
На данный момент лишь несколько ведущих компаний в мире обладают технологиями, позволяющими создавать такие системы. Это объясняется тем, что для получения информации о работающих позициях необходимо подключаться к ним и наблюдать за их работой, а не искусственно создавать оптимальные условия для получения диагностической информации, как в случае с построением диагностических графиков. При этом клапан может большую часть времени перемещаться в пределах нескольких процентов, что делает невозможным применение классических методов анализа диагностических данных.
Производитель должен разработать математические модели работы регулирующей арматуры, которые могли бы с высокой точностью определять техническое состояние оборудования даже по таким незначительным перемещениям. Он должен описать ключевые индикаторы состояния (Key Perfomance Indicators, KPI, например, трение, фактический диапазон пружины, время отклика и т.п.), которые были бы явно связаны с изменением технического состояния оборудования, и добиться того, чтобы рассчитанные на основе математических моделей значения не зависели от амплитуды изменения управляющего сигнала. То есть для одного и того же клапана необходимо всегда получать очень близкие значения индикаторов KPI как при амплитуде в 0,3…0,5…0,9%…, так и при амплитуде в 10…15…25%… и т.д.
Для реализации этой задачи должен быть разработан программный продукт, который по расписанию с заданным временным интервалом подключается ко всем цифровым позиционерам и определенное время отслеживает работу арматуры. Затем он автоматически рассчитывает индикаторы, связанные с техническим состоянием оборудования, сохраняет их в БД, определяет наличие отклонений от нормы, и в случае выявления неисправности информирует о ней оператора с указанием возможных причин ее появления и способов устранения. Только в этом случае возможно получить непрерывную диагностику работающего оборудования и по максимуму задействовать функции современных цифровых позиционеров. Желательно, чтобы в такой системе для любой позиции была возможность просмотра сборочных чертежей и определения артикульных номеров запасных частей.
Если на предприятии уже используются цифровые позиционеры с функциями диагностики, основные затраты при внедрении такой системы будут связаны с покупкой лицензии и с первичной настройкой. В ходе такой настройки для каждой позиции определяются допуски по каждому индикатору KPI. Да,здесь, как правило, не обойтись без привлечения специалистов поставщика оборудования/системы диагностики, но когда система настроена, затраты, связанные с ее обслуживанием, практически отсутствуют, так как не требуется персонал, обладающий глубокими познаниями в сфере диагностики, а основная часть операций выполняется в автоматическом режиме.
Преимущества подхода:
- позволяет следить за техническим состоянием оборудования в РВ;
- позволяет определять причины возникших неисправностей;
- для анализа не требуется наличие квалифицированного опытного специалиста.
Таким образом, если на предприятии с помощью диагностики планируется только определять износ сальникового уплотнения или контролировать исправность самого позиционера, то нет смысла приобретать дорогие позиционеры с расширенными диагностическими функциями.
Если же требуется хороший инструмент для оценки технического состояния регулирующей арматуры на время ремонтов, тот здесь не обойтись без позиционеров, которые могут строить диагностические графики. При этом стоит отдавать предпочтение продуктам, которые могут строить график зависимости положения клапана от давления в приводе, и обладают встроенными датчиками давления на выходе.
В случаях, когда принято решение постоянно следить за изменением технического состояния оборудования, стоит обратить внимание на позиционеры с расширенными диагностическими функциями и системы on-line диагностики. И если на предприятии эксплуатируются позиционеры нескольких производителей, то желательно выбирать программные продукты, которые могут работать одновременно со всеми имеющимися позиционерами.
С технологиями диагностики пневмоприводной арматуры предлагаем ознакомиться на странице сервисных услуг по обслуживанию арматуры - Диагностика регулирующей пневмоприводной арматуры
Автор статьи: Р.В. Городнев (ЗАО «ДС Контролз»)
Другие статьи